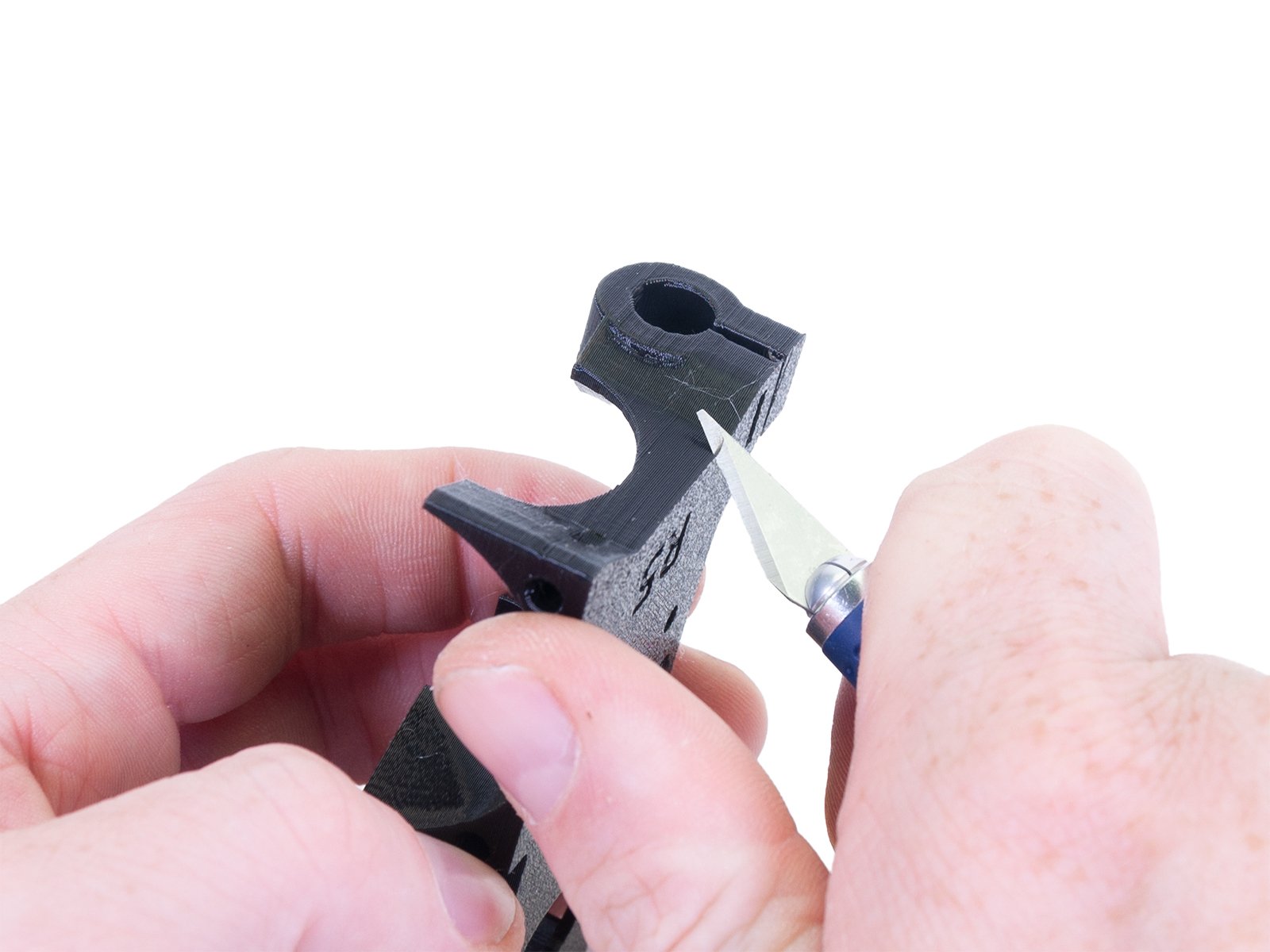
⬢This guide will explain in detail, how to post-process printed parts used on Original Prusa i3 printers to ensure easy assembly afterwards.
⬢Some printed parts designed for Original Prusa printers require post-processing. Skipping this part might cause issues and damage to the parts during the assembly.
⬢3D printing is a very accurate manufacturing process, but there are some factors, which can affect the final printed part:
⬢Temporary supports - must be removed after the print
⬢Different material properties - not all PETG or ABS are equal
⬢Defects in prints - strings, imperfections due to the geometry