The Prusa FFF printers are equipped with a brass nozzle. This article will review the main information about the nozzles that can be used with your printer.
Brass has excellent heat conductivity and is tough enough to print most "everyday" filaments. It is also accessible and reasonable to manufacture, which is probably why many 3D printers are supplied with brass nozzles.
Besides the standard 0.4 mm diameter, there are configurations for 0.25 mm, 0.6 mm, and 0.8 nozzle diameters. For the Prusa CHT brass nozzle, we offer the 0.4 mm, 0.6 mm, and 0.8 mm. On top of that, you can always create and customize your profiles. To achieve fine detail, you can use a 0.25 mm nozzle. We recommend using it only for small objects, a few centimeters in size, as the print times are considerably longer compared to 0.4mm nozzles. By contrast, if you want to speed up the print and the details are not as important, you can try using the 0.6 or 0.8 mm nozzle.
Standard nozzle | Printer |
---|---|
E3D 0.4 mm | MK2/S, MK2.5/S, MK3/S/+, MK3.5/S |
E3D-compatible brass nozzle 0.4 mm | MINI/+ |
Prusa Nozzle 0.4 mm | MK3.9, MK4, XL |
Prusa Nozzle Brass CHT 0.4 mm | MK3.9S, MK4S, XL |
If you need to change or replace the nozzle, please refer to our guides:
- MK2.5/S, MK3/S/+, MK3.5/S
- MINI/+
- MK4S, MK3.9S
- MK4, MK3.9
- Nozzle adapter for MK4/MK3.9
- XL Single-Tool, XL Multi-Tool
- Nozzle adapter for XL Single tool
E3D nozzles
The E3D (or E3D compatible) nozzles fit into the MK3/S/+ printer hotend (and all Prusa printers before it) and the MINI/+ hotend. This nozzle needs to be tightened while the hotend is heated, or there will be a gap between the nozzle and the heatbreak that the filament will leak out of. The filament is led into the heatbreak through a PTFE tube.
This nozzle can fit into the Nextruder with the Prusa Adapter, which also needs to be tightened while hot.
Prusa Nozzle Brass

The Prusa nozzle is also made of brass and its tip has the same internal geometry as the E3D-style nozzle. But in this nozzle, the heatbreak is attached to the nozzle so there is no need to heat the hotend to install the nozzle. It is also not necessary to have a PTFE tube to lead the filament into the nozzle.

Prusa Nozzle Brass CHT
The Bondtech CHT (Core Heating Technology) nozzles are designed to improve the efficiency of 3D printing and overcome traditional nozzles' limitations, particularly in filament flow. The internal design includes a split core that divides the filament into three streams within the nozzle. As a result, the surface area exposed to heat exponentially increases, leading to faster heating and a more consistent temperature across the entire filament width.
This enhanced heating process allows higher printing speeds while maintaining output consistency and quality. The nozzles can operate effectively even at lower temperatures than conventional ones because the heat is distributed more evenly and quickly.
This is especially advantageous when printing large objects or using materials that require high melting temperatures. Improved control over the temperature and filament flow can also lead to finer details and a higher-quality surface finish on printed objects, which is beneficial when printing models with intricate details.
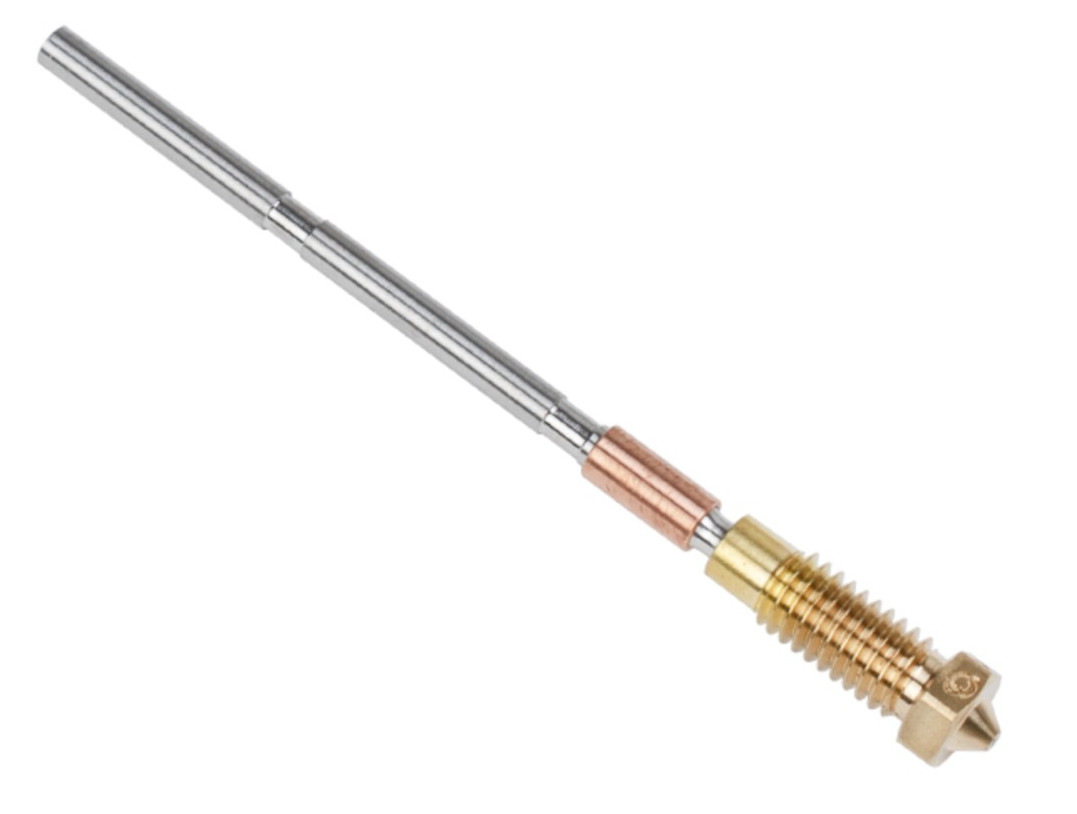
Identify nozzle size
You can identify the nozzle diameter by the dots around the rim of the nozzle. For example, the E3D 0.4 mm nozzles shipped with the Original Prusa MK3S+ have three dots (blue arrows).
Note that the E3D V6 0.25 mm nozzle has no dots, and looks almost the same as the E3D compatible 0.4 mm nozzle that ships with the Original Prusa MINI/+.
The markings apply to all E3D V6 nozzle types (brass, hardened, X), the Prusa Nozzle, and the Prusa Nozzle Brass CHT. Nozzles from other manufacturers may not have the same markings.
![]() | ![]() |
Nozzles for abrasive materials
Some filaments have particles added to them that can make them abrasive. A regular brass nozzle will degrade quickly and lose its properties when printing these. To print them, you will need to use a nozzle made of another material
Most of the abrasive materials are composites and plastics with additives. Some examples are ColorFabb XT CF20, ColorFabb Bronzefill, ColorFabb SteelFill, and some glow-in-the-dark filaments. Always ask your filament vendor if you are not sure about filament requirements. A slight disadvantage of the hardened steel nozzle is that some standard materials like ABS cannot be printed as fast as a regular nozzle. Due to the different thermal properties of a hardened steel nozzle compared to a brass nozzle, you may have to increase the nozzle temperature when printing.
Prusa Nozzle ObXidian
The ObXidian Nozzle is a high-quality nozzle designed specifically for abrasive materials and printing at high temperatures. It is made from hardened steel with a corrosion-resistant coating, ensuring exceptional durability and longevity.
These nozzles are particularly suitable for printing with abrasive materials like carbon fiber, as they maintain their hardness even at higher temperatures, delivering excellent performance and extending the lifespan of your nozzle.

Hardened steel nozzle by E3D
E3D, a UK-based company, that supplies hotends for the Original Prusa i3 printers, has a whole ecosystem of upgrades and add-ons. We support some of them, including the hardened steel nozzle.

Nozzle X by E3D
Nozzle X is a nozzle designed to address the thermal limitations of a hardened steel nozzle and the poor abrasion resistance of plated copper or brass nozzles. It is coated with WS2, a poly-phobic coating, that reduces the amount of plastic that sticks to the inside of the nozzle. For this reason, Nozzle X should not be maintained the same way as hardened steel or copper nozzles.
It can be used with abrasive fillers like glass, kevlar, or carbon reinforcement, but does not support more abrasive fillers, like Boron Carbide, Boron, Boron Nitride, Tungsten, or Tungsten carbide.

Recommended cleaning methods:
- Non-abrasive cloth/rag for external use.
- Cleaning filament for internal use.
Non-recommended cleaning methods:
- An acupuncture needle or a brass brush can damage the coating.
- Cold-pulls. Can tear off the WS2 coating.
The Olsson Ruby nozzle
Similar to the hardened steel nozzle, The Olsson Ruby is designed to print highly abrasive materials. Since it is mostly made of brass, it retains the excellent heat conductivity and throughput of the stock brass nozzle, but with a very hard gemstone as its tip. Even though the ruby gemstone is highly wear-resistant, it’s also brittle. If you have the Live Z adjust value set incorrectly, or if your PINDA sensor is not set to a correct distance and the nozzle hits the removable steel sheet, the nozzle may crack. For installation, please refer to the official 3DVERKSTAN instructions, as its installation is a bit more involved.
Other nozzle diameters
If you want to use a nozzle with a different diameter than the ones we already mentioned, you have to create the profile in PrusaSlicer manually. Starting with your standard 0.4 mm nozzle, you have to change the nozzle diameter in the Printer Settings and Extrusion width (percentage-wise). Keep in mind that the maximal layer height is always around 80% of the nozzle diameter. For more information, please see Creating profiles for different nozzles.
A 0.1 mm nozzle can be considered experimental; Its small diameter will not work with all filaments, the tolerances required in its manufacturing are hard to guarantee and the excessive printing time it requires can be beyond reasonable. For these fine resolutions, you may want to consider SLA printing.
PrusaSlicer configuration
To adjust preset settings in PrusaSlicer, go to Menu -> Configuration -> Configuration Wizard -> Prusa Research and select the printer model you have as well as the nozzle diameter you are currently using (purple squares).
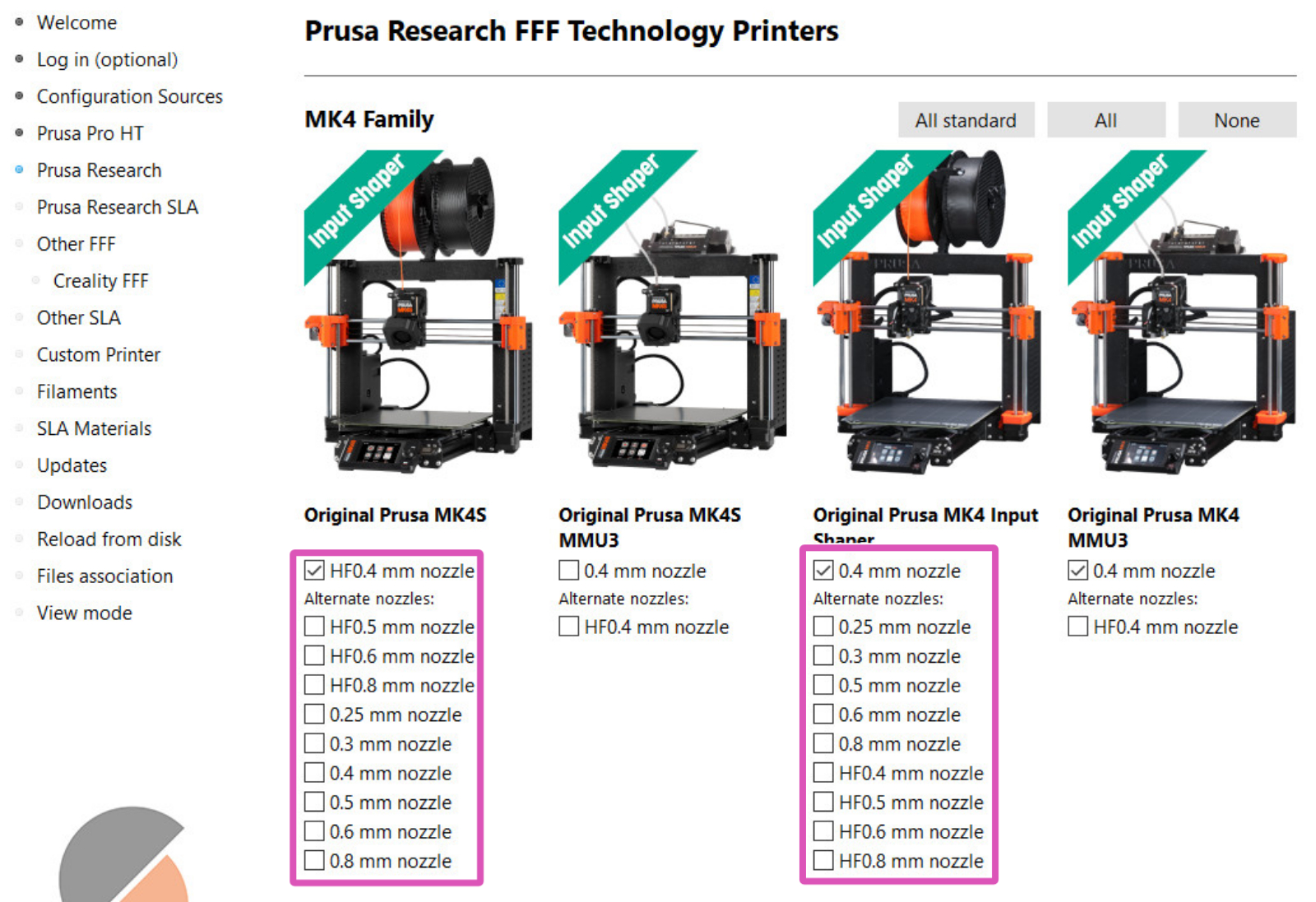
Unclick all the other models and nozzle diameters to avoid confusing the presets. You can always do the Wizard again and modify the settings. To set a different nozzle size on your printer, please see HW setup (MK2.5/S & MK3/S/+).
On MINI/+, MK4/S, XL, navigate to Menu -> Settings -> Hardware.
Except for the presets for the stock 0.4 nozzle, all other nozzle configurations will have the diameter stated in the name of the profile. If you don't have the words "0.25 nozzle", "0.6 nozzle" or "0.8 nozzle" in the profile's name (green square), the preset is for a 0.4 mm nozzle.

First Layer Calibration of other nozzles
Starting from firmware 3.13.0, the First Layer calibration works for multiple nozzle sizes. The nozzle size can be changed at Settings -> HW setup -> Nozzle d. [0.25|0.40|0.60|0.80]. The 0.4 mm nozzle is the default.
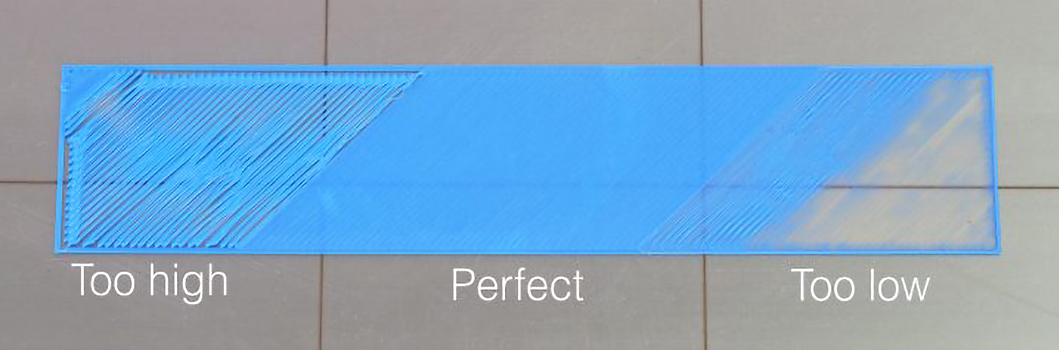
Reset Live Adjust Z value:
- Original Prusa MK3S+/MK3S/MK2.5S - Reset your Live Adjust Z value from LCD menu -> Settings -> Live Adjust Z, then scroll the selector knob clockwise until the value reaches zero.
- Original Prusa MINI - Reset your Live Adjust Z value from LCD menu -> Calibration -> Live Adjust Z, then scroll the selector knob clockwise until the value reaches zero.
- Original Prusa MK4, XL - These models are equipped with a Loadcell. If any Live Adjust Z value is set, this is automatically reset after the next print is done.
After this, start your G-code and 'Adjust Live Z' while printing:
- Press the knob after it has started extruding and locate 'Adjust Live Z'.
- Select it and turn the knob clockwise until the line is flattened, but not squished. It should have a smooth top. When doing solid top-fill, make sure there are neither gaps between the lines (too far away), nor ridges between the lines (too close). Please see First Layer Calibration (i3) or First Layer Calibration (MINI/MINI+) for examples.
- Press the selector knob again to store the value.
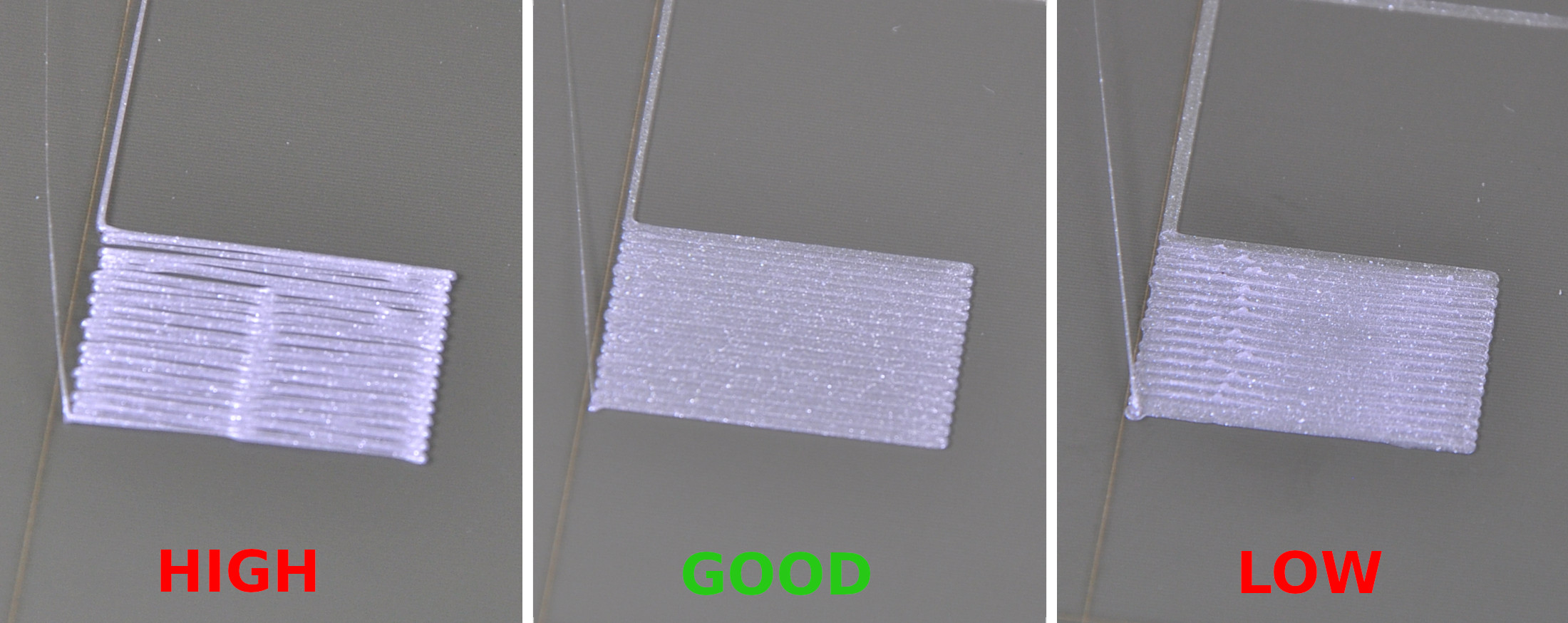
The image depicts the first layer of a 0.4 mm nozzle. The line can be almost half the width of what is depicted.
Other considerations
Smaller diameters (~0.25 mm)
Almost any Composite material is out of the question. The particles in it can (and will) quickly clog or ruin your nozzle. However, filaments with fine glitter or similar "shine particles", like what is found in Prusament Galaxy Silver, should be no problem.
Flexible materials can also be problematic on a smaller diameter nozzle due to the higher pressure required for extrusion. It can buckle and tangle around the filament pulleys with higher pressure.
Slow speed - Precision takes time, prepare yourself for printing times of 24 to 100 hours, even with smaller objects. Not only is each line thinner and narrower than usual, which results in more perimeters, but the extruder movements are also greatly reduced to accommodate the increased accuracy.
When printing with a smaller nozzle, calibration and bed leveling become even more important. After changing the nozzle, make sure you at least run the Z calibration of your printer before you start printing.
Larger diameters (>0.6 mm)
The main drawback is its resolution. The thicker and taller layer lines will print the object faster but will have limitations in regards to fine details. On the other side, functional parts may prove stronger since each line has a larger amount of solid material.
Also, thanks to the larger nozzle diameter there will be more solid material to cool down which may increase warping. This might be an issue for materials prone to warping during print, like ABS or PC Blend.
Nozzle size / Material | 0.25 mm | 0.4 mm | 0.6/0.8 mm |
Flexible materials | ✖ | ✔ | ✔ |
PLA | ✔ | ✔ | ✔ |
ASA/ABS | ✔ | ✔ | ✔ |
PETG | ✔ | ✔ | ✔ |
wood/metal infused | ✖ | ✔ * | ✔ |
CF/kevlar infused ABS | ✖ | ✔ * | ✔ * |
PC Blend | ✔ | ✔ | ✔ |
Nylon | ✔ | ✔ | ✔ |
PVA/BVOH | ✖ | ✔ | ✔ |
* Hardened nozzle
22 comments
* Is there any performance difference between the two?
* Is there any way to discuss any differences on the internal geometries or other techniques to enable high flow without violating any NDAs?
* One weakness of CHT nozzles is the difficulty of cleaning jams because of the multi-path internal geometry. Does the E3D nozzle share that weakness or have a similar weakness?
Hello. The standard nozzle has 'PR' printed on it, while the CHT nozzle has 'CHT' printed on it. Additionally, the CHT nozzle has a Bondtech logo on one side of the head (where the dots are).