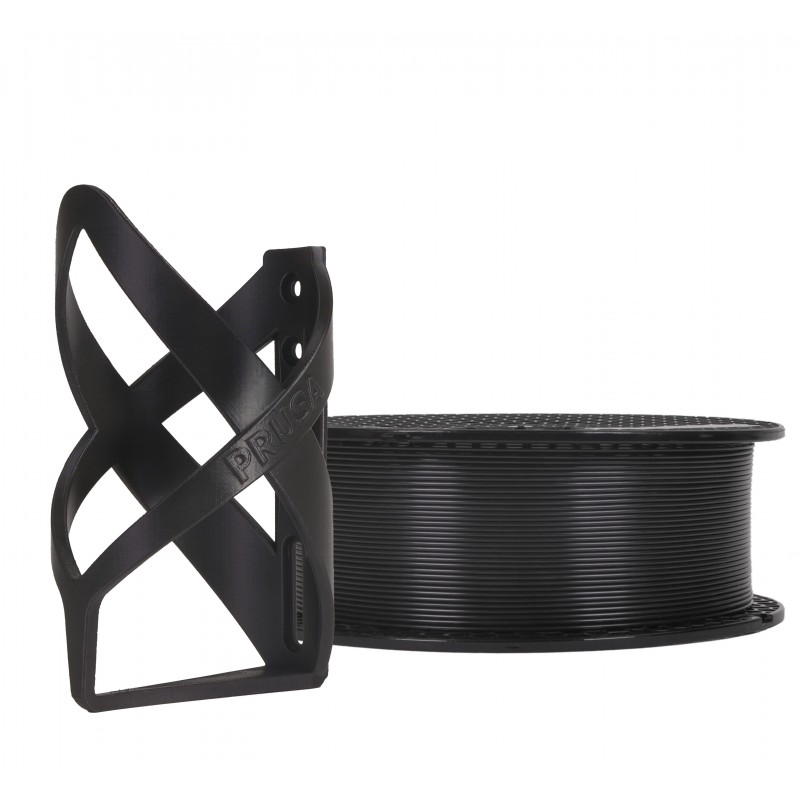
Basic info
Description
ASA (Acrylic Styrene Acrylonitrile) is a technical material that is considered a successor to ABS. Compared to ABS, ASA is more UV resistant, warps less, and doesn’t smell as much. ASA is a tough and resilient material that is, thanks to its UV and temperature resistance (up to 93 °C), suitable for outdoor use and for making technical parts. Another great advantage of ASA is its solubility in acetone, which can be used to make a smooth and glossy finish. This gives the model not only great looks but also different mechanical properties (see our article about chemical smoothing).
The main disadvantage of ASA is significant warping caused by temperature differences between the model and its surroundings. Another disadvantage is that ASA releases potentially dangerous fumes during printing - this means you should keep your printer in a well-ventilated area. ASA can be easily sanded both wet and dry.
You can find more details about how to print with ASA in our in-depth article.
And to compare supported material properties, see our material table.
Pros |
Cons |
---|---|
✔ High UV resistance |
✖ Significant warping |
✔ Good high-temperature resistance |
✖ An enclosure is necessary for printing large parts |
✔ Detailed prints with no stringing |
✖ Potentially dangerous fumes (styrene) |
✔ Possibility of acetone smoothing and gluing |
✖ Prints at high temperatures |
✔ Easy postprocessing (e.g., sanding, cutting, etc.) |
✖ Partially hygroscopic (absorbs moisture) |
✔ High impact and wear resistance |
Best use
ASA is suitable for outdoor use and for making technical parts.
Tips for successful printing
Try to keep a high ambient temperature
The bed should be heated to at least 100 °C, and the printer should be inside an enclosure to keep a higher ambient temperature. If you don’t have an enclosure, there’s one simple alternative: in PrusaSlicer, use the draft shield option (Print Settings/Skirt & Brim). This will create a wall around the object and keep the model slightly warmer, mitigating the warping. Keep in mind that printing a lot of ASA in an unventilated enclosure can cause the fan shroud and/or extruder plastic parts to deform over time. This may impact performance or cause issues.
It is also possible to make your own enclosure.
ASA sticks very well to our print sheets (smooth and powder coated) but other print surfaces, like glass, might require a layer of acetone with dissolved ASA (or ABS).
Chemical smoothing
ASA is a pretty good material for postprocessing. Not only can you sand it wet and dry but you can also glue/weld it with acetone and smooth it with acetone vapors. Smoothed models have a glossy surface that looks like it’s treated with car lacquer or was injection molded. However, printed objects usually tend to lose detail and sharp edges with smoothing. You can find out more about chemical smoothing in article about chemical smoothing.
Sample prints
![]() | ![]() |
Mechanical parts | Acetone smoothed prints |
![]() | ![]() |
Fan shroud (high-temperature resistant parts) | Outdoor (UV resistant) parts |
7 comments
I always had problems with prusa's textured sheets and use them for PC only.You will definitely need an enclosure, or a Voron, hi, hi.